Robot from BILA Service Handles Heavy Lifting
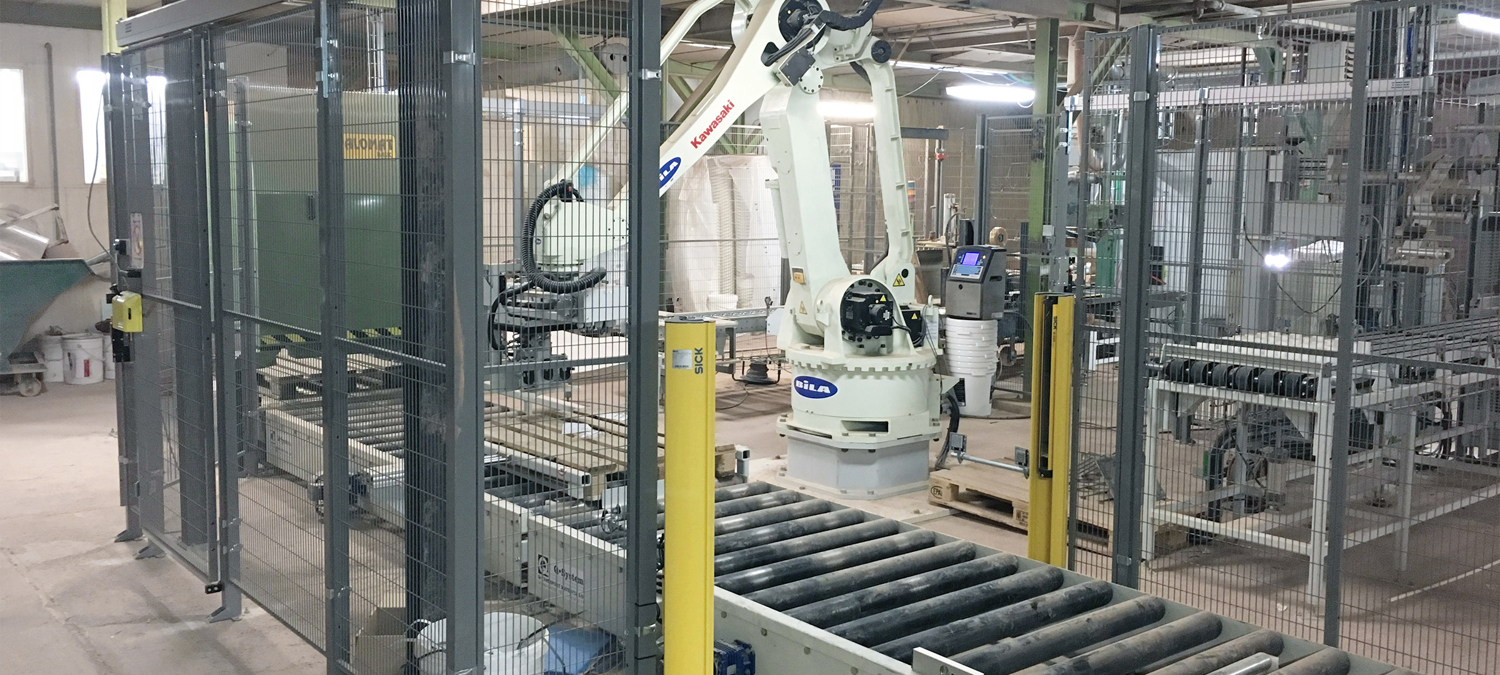
Flexible solution
The automation solution from BILA Service has streamlined production, reduced logistics costs, and improved the working environment for employees at Imery Absorbents' factory in Mors.
Palletizes 15 kg buckets
Flexible solution
Robot handles 3 production lines
Quick installation
Challenge
At Imery Absorbents, keeping up with demand has been a challenge. With an extensive range of product numbers and numerous small productions, palletizing the finished products has been a particular challenge.
Solution
The renovated and updated robot cell from BILA Service, a refurbished Kawasaki ZD 130 robot cell, now handles three production lines simultaneously and performs palletizing directly from the conveyor belt to a pallet station.
Profit
Thanks to the possibility of easy reconfiguration according to the product type, the production process is significantly more flexible today compared to before. The solution has also contributed to eliminating heavy lifting.
Imery Absorbents (formerly Damolin) produces oil and chemical absorbents as well as powder and granulate products through mining and processing of naturally occurring minerals and complementary products. Over the years, the company, which was acquired by the French company Imerys in January, has expanded its product range, now providing customer-specific total solutions for both industrial and commercial sectors in Europe and overseas markets. In addition to the factory on Mors, Imerys also has a Danish factory on Fur.
Inflexible production line called for a new solution
Production is bustling at Imerys. So busy that at times, it has been challenging to keep up with demand. With many different product numbers and numerous small productions, palletising the finished products, among other things, posed a challenge. Until about a year ago, palletising three product types was done manually. This meant that an employee stood at a conveyor belt manually palletising, for example, 15 kg heavy buckets.
"We have always had the lifting equipment needed for such tasks, but manual palletising is still a very monotonous and heavy job,"
Rasmus Krog, Project Manager
He called for a solution that could relieve employees of monotonous work and, at the same time, make production more flexible.
Streamlined palletising brought more flexibility
In addition to the heavy buckets, an automated solution also had to handle large cartons with heavy sacks as well as filled sacks for baling (wrapping with foil before shipping products). The production line, which was previously operated manually, thus handled three different processes, placing great demands on easy reconfiguration and flexibility for an automation solution. But in December 2016, the solution was ready: a refurbished Kawasaki ZD 130 robot cell delivered by BILA Service.
The renovated robot cell now serves three lines and palletises the three productions directly from the conveyor belt onto a pallet station. And since the solution can be easily reconfigured for each product type, the production is much more flexible today.
"In collaboration with BILA Service, we created a system that can handle the three different productions. It has made us much more flexible and better able to quickly reconfigure our production for the three different productions depending on sales. Previously, we packed for inventory to meet delivery times because manual handling was slower," says Rasmus Krog.
No heavy lifting and much less overtime
He explains that the solution with the Kawasaki robot was developed in collaboration between Imerys' own technical department and BILA Service:
"Our blacksmiths and electricians have tremendous expertise in their field, and the same goes for BILA. The collaboration has resulted in a very sensible solution that has made our production significantly more flexible,"
Rasmus Krog, Project Manager
The robot cell from BILA Service has also excited employees in the production line. Not only are they relieved of heavy lifting, but overtime and weekend work have also been significantly reduced after palletizing was automated. Now, employee hours can be allocated to other tasks, and production can take place within normal working hours—all while the products leaving the factory continue to be delivered on time.
Get 360 degree consultation about your setup, and let us help you elevate your automation aspirations to the next level.
You can contact us at +45 97 71 00 44.
Contact us
We are ready to answer all your
questions and have a non-committal
conversation about the possibilities
with production optimisation in your company.