Automation Helps Carlsberg in the Fight for Zero Work-Related Accidents
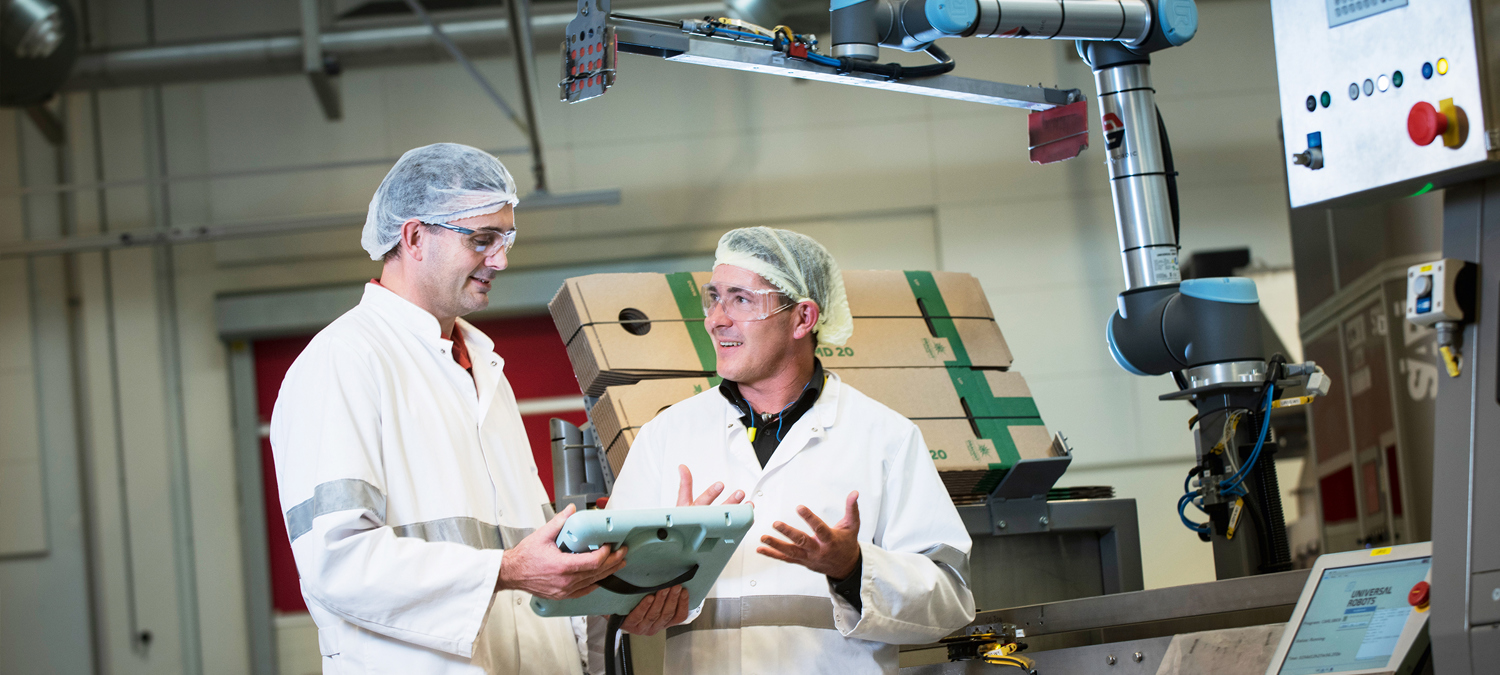
Highly automated production line
Two robot arms from Universal Robots are helping brewers at Carlsberg's brewery in Fredericia to eliminate the remaining manual work processes on the already highly automated production line. The robots have freed up nearly 50% capacity on the line and brought Carlsberg a step closer to the goal of zero accidents.
Released approx. 50% capacity
Freed up employee hours
500 packaging cartons per hour
Increased employee well-being
Challenge
In Carlsberg's sustainability program, there is a goal to achieve zero workplace accidents in production. Additionally, there was a goal to minimise repetitive and monotonous tasks that risked wearing down individual employees. To achieve these goals, Carlsberg in Fredericia explored automation solutions.
Solution
Two UR robots have now been implemented in production. A UR10 robot arm grabs a stack of 10 cartons, bound together with a strap, and transports it to the second robot. The UR3 robot cuts the strap and lowers it into a waste bag. Then, the UR10 robot takes over again, placing the stack in an empty magazine that continues into a case erector for carton filling.
Profit
The investment in the two robot arms was not primarily to increase production capacity but rather to lighten the load for employees and improve their working environment. Carlsberg's goal is to achieve zero accidents, and the robots play a crucial role in helping them reach this goal.
Two additional robots for production
In the fall of 2017, Carlsberg Brewery in Fredericia acquired two additional arms for production: two UR robots that handle up to 500 packaging cartons per hour on a line packing bottles and cans with the world-famous beers.
”The entire line where the UR robots are located now consists of highly automated technology for draft beer. We want to stay ahead of the curve to brew for today and tomorrow. That's our goal,”
Thomas Kern Ruby, Senior Project Manager
Originally, the new line was designed without the UR robots, meaning a person stood and lifted packaging cartons from a pallet and placed them in a magazine.
”The high degree of automation means human involvement on the line is at an absolute minimum. Therefore, we hope that we are one step closer to avoiding accidents entirely, which is a central element in Carlsberg's sustainability program. We want to take care of our employees, and the new UR robots eliminate repetitive, strenuous, and one-sided lifting tasks,” says Thomas Kern Ruby. It quickly became clear that packaging handling also needed to be automated. So it was.
”We inquired with various robot manufacturers, and it turned out that the UR robots were perfect for the task, partly because they work so smoothly and do not require fencing,” says Thomas Kern Ruby, Senior Project Manager.
Collaboration led to optimal solution
After being contacted by Carlsberg Fredericia, BILA Robotics Area Manager Steen Slabiak Jensen initially held a small workshop for Carlsberg's technicians and management:
”At first, it was about getting the employees to understand the benefits of collaborative automation versus automation with large industrial robots, which is often a much more complex, slow, and heavy process,” says Steen Slabiak Jensen, BILA Robotics Area Manager.
He then contacted a partner from the automation company Robot Nordic and told him about the task. Together, they visited the brewery in Fredericia for a more in-depth inspection and collaboratively developed the final solution, which Robot Nordic successfully implemented in the fall of 2017.
Today, two UR robot arms prepare the packaging cartons for packing beer products on the highly automated line in Carlsberg production. First, a UR10 robot arm grabs a stack of 10 cartons, bound together with a strap, and lifts the stack to the second robot arm, a UR3. This robot cuts the strap and lowers it into a waste bag. Then, the UR10 takes over again, placing the stack in an empty magazine that continues into a case erector, after which the cartons are filled.
”Carlsberg is a specialised company. We knew we had to deliver the best of the best. It was demanding, but there has been a super good and constructive collaboration between all parties,”
Steen Slabiak Jensen, BILA Robotics Area Manager
Improved work environment
Since January 2009, the majority of Carlsberg's beer and soft drink production for the Danish market has been consolidated at the brewery in Fredericia, which is now one of the area's largest workplaces with over 800 employees and an annual production that reached 6.5 million hectoliters in 2017. For the Carlsberg brewery in southern Jutland, the investment in the two UR robots was not about increasing production capacity but rather about using employee resources more efficiently and relieving employees of monotonous tasks.
”Our primary bottleneck has always been the filling of bottles and cans because that process cannot be faster without compromising the product, and we never compromise on quality," says Thomas Kern Ruby, explaining that the UR robots were purchased with the desire to use employee capacity more efficiently and improve the working environment on the line.
"The investment in the two UR robots has not been about increasing production capacity but about relieving employees and improving their working environment. In Carlsberg's sustainability program, we have an ambition of zero accidents, and the robots help with that. Primarily by automating a monotonous task that, in addition to an inconvenient working position, also involved handling a knife and therefore a risk of cuts,” says Thomas Kern Ruby, Senior Project Manager.
Before, the task took up 70-80% of one employee's capacity at the line; today, the employee's only task in connection with packaging handling is to bring a pallet with cardboard boxes to the line. The robots handle the rest. This has meant that the line can now be managed by two operators without any issues, continuously performing tasks such as testing, hygiene, troubleshooting, etc.
Get 360 degree consultation about your setup, and let us help you elevate your automation aspirations to the next level.
You can contact us at +45 97 71 00 44.
Contact us
We are ready to answer all your
questions and have a non-committal
conversation about the possibilities
with production optimisation in your company.